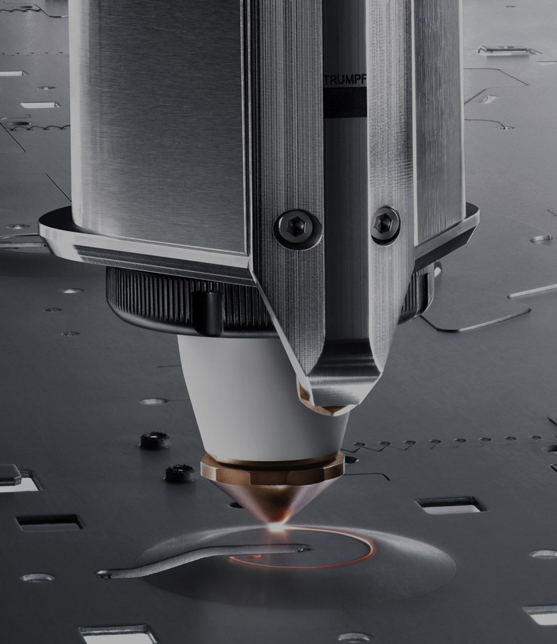
small cnc metal lathe is an advanced manufacturing process that uses computer-controlled machines to shape and cut metal materials. Utilizing computer numerical control (CNC) technology, these machines can be programmed to follow specific design instructions to produce precise and complex shapes, resulting in high-quality Phosphorus bronze parts.
In the small cnc metal lathe process, a computer program generates a set of instructions, or code, which are then sent to the machine's controller unit. The code contains information about the specific tools, speeds, and feeds required to create the required part. The machine's movements are then controlled by a computer, following programmed instructions to produce a final product with incredible precision. Thanks to advanced technology and automated controls, metal CNC machines can operate continuously and require minimal human intervention. This increases production efficiency, reduces labor costs, and shortens turnaround time for finished parts.
CNC Machining or Not | small cnc metal lathe |
Material Capabilities | Aluminum, Brass, Copper, Hardened Metals, Precious Metals, Stainless steel, Steel Alloys |
Type | Laser Machining, Milling, Other Machining Services, Turning, Rapid Prototyping |
Surface treatment | Color Anodize,Sandblasting,Powder Coating,Electroplating,Zink Plating |
Tolerance | 0.005-0.01mm |
Process | Cnc Machining + Surface Treatment |
Equipment | Milling Machine :3/4/5 Axis CNC Machining Center:Turning Centre |
Quality Control | ISO/TS9001 |
Name | Custom Machining Metal Parts Service |
Place of Origin | China |
small cnc metal lathe FAQs Guide. we will delve into the specifics of small cnc metal lathe machining and explore its advantages, applications, and key considerations for successful implementation. Whether you are new to the field or looking to expand your knowledge, this guide will provide a comprehensive overview of this revolutionary manufacturing process. So, let's begin our journey into the world of small cnc metal lathe machining!
1.About small cnc metal lathe raw material procurement system
A metal CNC raw material procurement system is a computerized system that helps to streamline the process of purchasing raw materials for CNC machining. The system helps to automate the process of ordering, tracking, and managing the raw materials needed for CNC machining. It also helps to ensure that the right materials are ordered in the right quantities and at the right time. The system can also help to reduce costs associated with purchasing raw materials, as well as improve the efficiency of the CNC machining process.
2.What are the different types of small cnc metal lathe machines available in the market?
We maintain a certain amount of R&D investment every year and continuously improve operational efficiency to provide better services to our cooperative customers. 1. Lathe CNC Machine: A lathe CNC machine is used for cutting, drilling, and turning metal parts. It is one of the most common types of CNC machines used in the manufacturing industry. 2. Milling CNC Machine: A milling CNC machine is used for cutting, drilling, and shaping metal parts. It is used for creating complex shapes and intricate details. 3. Plasma Cutting CNC Machine: A plasma cutting CNC machine is used for cutting metal parts with a high-temperature plasma arc. It is used for creating intricate shapes and details. 4. Laser Cutting CNC Machine: A laser cutting CNC machine is used for cutting metal parts with a high-powered laser beam. It is used for creating intricate shapes and details. 5. Waterjet Cutting CNC Machine: A waterjet cutting CNC machine is used for cutting metal parts with a high-pressure stream of water. It is used for creating intricate shapes and details.
3.What are the different types of tool changes used in small cnc metal lathe machining?
1. Manual Tool Change: This is the most basic type of tool change and involves manually exchanging the cutting tool by hand. 2. Automatic Tool Change: This type of tool change is automated and is typically used in CNC machining centers. The tool is automatically exchanged by a robotic arm or a tool changer. 3. Quick Change Tooling: This type of tool change is used in CNC lathes and involves a quick-change tool holder that allows for rapid tool changes. 4. Tool Presetter: This type of tool change is used in CNC machining centers and involves a tool presetter that measures the tool and sets it to the correct position before it is used.
4.What is the role of coolant in reducing heat and friction during small cnc metal lathe machining?
Our small cnc metal lathe products undergo strict quality control to ensure customer satisfaction. Coolant plays an important role in reducing heat and friction during metal CNC machining. Coolant helps to reduce the temperature of the cutting tool and the workpiece, which helps to reduce the amount of heat generated during the machining process. Coolant also helps to reduce friction between the cutting tool and the workpiece, which helps to reduce wear and tear on the cutting tool and the workpiece. Additionally, coolant helps to flush away chips and debris from the cutting area, which helps to reduce the risk of clogging and jamming.
5.Can small cnc metal lathe machines be used for both large and small scale production?
small cnc metal lathe is not a product only, but also can help you comes to money-making. Yes, metal CNC machines can be used for both large and small scale production. CNC machines are highly versatile and can be used to produce a wide range of products, from small components to large-scale parts. The size of the parts that can be produced is only limited by the size of the machine and the tools that are used.
6.What safety precautions should be taken when handling metal pieces in a CNC machine?
We are a professional small cnc metal lathe company dedicated to providing high quality products and services. 1. Wear protective clothing, such as safety glasses, gloves, and a face shield. 2. Ensure that the machine is properly grounded and that all electrical components are in good working order. 3. Make sure that the machine is properly lubricated and that all moving parts are free of debris. 4. Keep hands and other body parts away from the cutting area. 5. Use a vacuum to collect any metal chips or shavings that may be created during the machining process. 6. Make sure that the cutting tools are sharp and in good condition. 7. Use a coolant to reduce heat buildup and to reduce the risk of fire. 8. Make sure that the workpiece is securely clamped in place before machining. 9. Make sure that the machine is turned off and unplugged when not in use. 10. Make sure that the machine is properly maintained and inspected regularly.
7.About small cnc metal lathe MOQ
The MOQ for metal CNC machining depends on the complexity of the part and the material used. Generally, the MOQ is between 1 and 10 pieces. However, some suppliers may offer lower MOQs for certain parts or materials.
8.What are the common mistakes made when programming a small cnc metal lathe machine?
We have established long-term and stable partnerships with our suppliers, so we have great advantages in price and cost and quality assurance. 1. Not double-checking the program before running it. 2. Not accounting for the tool’s diameter when calculating the cutting depth. 3. Not accounting for the tool’s length when calculating the cutting length. 4. Not accounting for the tool’s speed when calculating the feed rate. 5. Not accounting for the material’s hardness when calculating the cutting speed. 6. Not accounting for the material’s thickness when calculating the cutting depth. 7. Not accounting for the material’s shape when calculating the cutting path. 8. Not accounting for the material’s surface finish when calculating the cutting speed. 9. Not accounting for the machine’s rigidity when calculating the cutting speed. 10. Not accounting for the machine’s accuracy when calculating the cutting path.
9.Is it possible to perform reverse engineering using small cnc metal lathe machining?
Yes, it is possible to perform reverse engineering using metal CNC machining. This process involves taking a physical object and using a CNC machine to create a 3D model of the object. This model can then be used to create a new version of the object or to modify the existing object.
10.What is the maintenance routine for a small cnc metal lathe machine?
We operate our small cnc metal lathe business with integrity and honesty. 1. Clean the machine regularly. 2. Check the lubrication levels and top up as needed. 3. Check for any loose bolts or screws and tighten them. 4. Inspect the cutting tools for wear and replace as needed. 5. Check the coolant levels and top up as needed. 6. Check the spindle bearings for wear and replace as needed. 7. Check the electrical connections and wiring for any signs of damage or wear. 8. Check the machine for any signs of vibration or excessive noise. 9. Check the machine for any signs of overheating. 10. Check the machine for any signs of corrosion or rust.
11.About small cnc metal lathe production equipment
Metal CNC production equipment is a type of computer-controlled machinery used to produce metal parts and components. It is used in a variety of industries, including aerospace, automotive, medical, and industrial. CNC production equipment is capable of producing complex shapes and intricate details with high precision and accuracy. It is also capable of producing parts with tight tolerances and repeatability. CNC production equipment is used to produce parts for a variety of applications, including automotive, aerospace, medical, and industrial.
12.About small cnc metal lathe customization services
Metal CNC customization services are a great way to create custom parts and components for a variety of applications. CNC stands for Computer Numerical Control, and it is a process that uses computer-controlled machines to cut and shape metal into the desired shape. CNC machines are used in a variety of industries, including aerospace, automotive, medical, and industrial. CNC customization services can provide custom parts and components that are designed to meet the exact specifications of the customer. These services can also provide a variety of finishes, such as anodizing, powder coating, and plating. CNC customization services can also provide a variety of machining services, such as drilling, tapping, and milling.
13.About small cnc metal lathe production skills training
Metal CNC production skills training is a type of training that teaches individuals how to use CNC machines to produce metal parts. This type of training is typically offered by technical schools, community colleges, and other educational institutions. It can also be offered by companies that specialize in CNC production. The training typically covers topics such as machine setup, programming, and operation. It also covers safety procedures and quality control.
14.Can small cnc metal lathe machines be integrated with robotic arms for automation?
Yes, metal CNC machines can be integrated with robotic arms for automation. This is becoming increasingly popular in the manufacturing industry as it allows for more efficient and precise production. The robotic arms can be programmed to perform specific tasks such as loading and unloading materials, as well as performing complex machining operations.
15.About the development history of small cnc metal lathe factory
Metal CNC factories have been around since the early 1950s. The first CNC machines were developed in the United States by John T. Parsons and John H. Parsons. These machines were used to produce precision parts for the aerospace industry. In the 1960s, CNC machines began to be used in the automotive industry, and by the 1970s, CNC machines were being used in a variety of industries. Today, CNC machines are used in a wide range of industries, from aerospace to medical to automotive. CNC machines are used to produce parts with high precision and accuracy, and they are used in a variety of applications, from prototyping to production.
16.About small cnc metal lathe raw materials
Metal CNC raw materials are typically metals such as aluminum, steel, brass, and copper. These materials are used to create parts and components for a variety of applications, including automotive, aerospace, and medical. The raw materials are cut and shaped using CNC machines, which are computer-controlled machines that use a variety of tools to cut and shape the material. The raw materials are then machined and finished to create the desired product.
17.About the scale of small cnc metal lathe factory
The size of a metal CNC factory depends on the type of products it produces and the size of its customer base. A small factory may only have a few CNC machines and a few employees, while a larger factory may have dozens of CNC machines and hundreds of employees. The size of the factory also depends on the type of materials it works with, as some materials require more specialized equipment than others.
18.What are the advantages of using computer control in small cnc metal lathe machining?
We focus on teamwork and communication to achieve common goals, We attach great importance to this detail. 1. Increased Accuracy: Computer control allows for more precise machining than manual machining. This is because the computer can be programmed to make very precise cuts and can be adjusted to account for any errors that may occur. 2. Increased Speed: Computer control allows for faster machining than manual machining. This is because the computer can be programmed to make multiple cuts at once and can be adjusted to account for any errors that may occur. 3. Increased Efficiency: Computer control allows for more efficient machining than manual machining. This is because the computer can be programmed to make multiple cuts at once and can be adjusted to account for any errors that may occur. 4. Reduced Waste: Computer control allows for less waste than manual machining. This is because the computer can be programmed to make multiple cuts at once and can be adjusted to account for any errors that may occur. 5. Increased Safety: Computer control allows for safer machining than manual machining. This is because the computer can be programmed to make multiple cuts at once and can be adjusted to account for any errors that may occur.
19.What are the most commonly used cutting tools in small cnc metal lathe machining?
We have established long-term and stable partnerships with our suppliers, so we have great advantages in price and cost and quality assurance. 1. End Mills: End mills are the most commonly used cutting tools in metal CNC machining. They are used to cut slots, pockets, and contours in a variety of materials. 2. Drills: Drills are used to create holes in a variety of materials. They are available in a variety of sizes and shapes to accommodate different applications. 3. Reamers: Reamers are used to enlarge existing holes in a variety of materials. They are available in a variety of sizes and shapes to accommodate different applications. 4. Taps: Taps are used to create internal threads in a variety of materials. They are available in a variety of sizes and shapes to accommodate different applications. 5. Countersinks: Countersinks are used to create a conical shape in a variety of materials. They are available in a variety of sizes and shapes to accommodate different applications.
20.How long does it typically take to master the skills of small cnc metal lathe machining?
Our products & services cover a wide range of areas and meet the needs of different fields. The amount of time it takes to master the skills of metal CNC machining depends on the individual and the complexity of the parts being machined. Generally, it can take anywhere from a few months to a few years to become proficient in CNC machining.