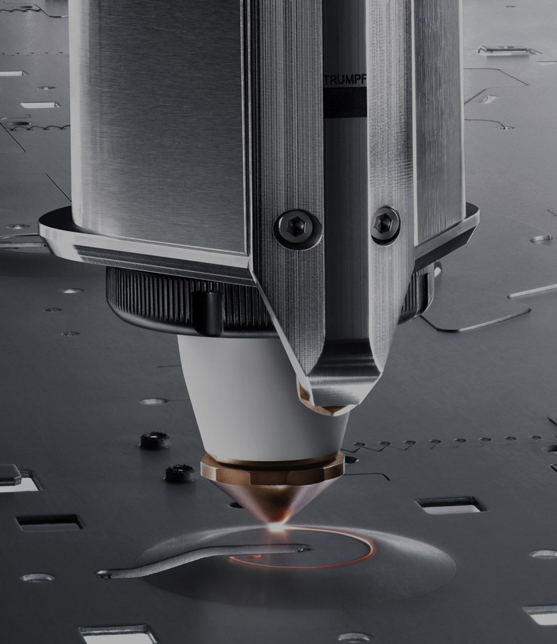
Xiamen Wiesel Technology Co., Ltd. is a manufacturer specializing in the production of precision metal parts for the automotive, aerospace, and medical industries. We have a strong R&D team and advanced CNC machine tools that can produce complex, high-precision parts. Wiesel has passed ISO9001 and ISO TS16949 certification to ensure product quality and reliability. We have been committed to technology promotion, R&D team training, and new process development.
Metal CNC technology can be used to process a variety of metal materials, including aluminum, copper, steel, stainless steel, etc., with a wide range of applications. It is also highly flexible and can process various complex shapes according to design requirements to meet the needs of different customers. The advantages of Metal CNC technology also include high efficiency and high stability. It can process multiple parts at the same time, improve processing efficiency and reduce production costs. Moreover, the use of high-quality cutting tools and materials ensures stable and reliable processing quality and greatly reduces product quality defects.
about 5 axis metal cnc, we have carefully prepared some relevant professional knowledge documents for you, {hope to provide some help to you who are interested in 5 axis metal cnc
Metal CNC is a high-precision CNC machining technology that can accurately control mechanical tools to process metal materials. Its accuracy and precision far exceed traditional machining methods. Through Metal CNC technology, precision processing of metal materials can be achieved, including the manufacturing of fine parts, processing of complex geometric shapes and high-precision surface treatment. The use of this technology will not only greatly improve production efficiency, but also make the quality of products more stable. It is widely used in various fields such as aerospace, automobiles, ships, and machinery manufacturing. Metal CNC technology gives powerful capabilities to high-precision machining and will bring more precise and higher-quality products to all walks of life.
With the continuous development of modern technology, CNC technology is receiving more and more attention. In the manufacturing process of various mechanical equipment, the application of Metal CNC technology has become an indispensable part. Compared with traditional processing methods, Metal CNC technology has higher accuracy and efficiency, and more importantly, its super durability. Through the precise cutting and engraving of metal materials, Metal CNC technology can produce precise and durable parts, thereby increasing the service life and performance of equipment. Whether it is automobiles, aircraft or electronic products, Metal CNC technology plays an important role in providing a stable and reliable foundation for the development of all walks of life. It is precisely because of its long-term advantages that Metal CNC technology is becoming the mainstream of modern manufacturing, bringing us more and better products and services.
Metal CNC--An Ultimate FAQ Guide.
1.How does the rigidity of the machine affect the outcome of metal CNC machining?
The rigidity of the machine affects the outcome of metal CNC machining in several ways. A rigid machine will be able to hold the cutting tool in a more precise position, resulting in more accurate cuts and better surface finish. A rigid machine will also be able to handle higher cutting forces, allowing for faster cutting speeds and deeper cuts. Finally, a rigid machine will be less prone to vibration, which can cause poor surface finish and inaccurate cuts.
2.About metal cnc overseas warehouse
Metal CNC overseas warehouses are warehouses located in foreign countries that specialize in the storage and distribution of metal CNC parts and components. These warehouses are typically owned and operated by a metal CNC manufacturer or distributor, and they provide a convenient way for customers to access parts and components from around the world. Metal CNC overseas warehouses are often located in countries with lower labor costs, allowing manufacturers to reduce their overhead costs and pass those savings on to their customers.
3.Is it possible to perform multiple operations on a single piece using metal CNC machining?
Yes, it is possible to perform multiple operations on a single piece using metal CNC machining. Depending on the complexity of the part, multiple operations such as drilling, milling, turning, and tapping can be performed on a single piece.
4.Can metal CNC machining be used for internal threading?
Yes, metal CNC machining can be used for internal threading. CNC machines are capable of producing a variety of thread forms, including straight, tapered, and buttress threads.
5.What is the role of coolant in metal CNC machining?
Coolant plays an important role in metal CNC machining. It helps to reduce friction between the cutting tool and the workpiece, which helps to improve the cutting performance and extend the life of the cutting tool. Coolant also helps to reduce heat generated during the machining process, which helps to prevent the workpiece from warping or cracking. Additionally, coolant helps to flush away chips and debris from the cutting area, which helps to improve the surface finish of the machined part.
6.Are there any environmental benefits to using metal CNC machining?
Yes, metal CNC machining can provide environmental benefits. CNC machining is a highly efficient process that produces very little waste, which helps to reduce the amount of material that needs to be disposed of. Additionally, CNC machining can be used to create parts with very precise tolerances, which can help to reduce the amount of energy needed to produce a part. Finally, CNC machining can be used to create parts with a longer lifespan, which can help to reduce the amount of materials that need to be replaced over time.
7.What is the difference between CNC milling and CNC turning?
CNC milling is a machining process that uses computer numerical control (CNC) to control the movement of a cutting tool to shape a workpiece. It is used to create complex shapes and features in a variety of materials. CNC turning is a machining process that uses computer numerical control (CNC) to control the movement of a cutting tool to shape a workpiece. It is used to create cylindrical parts with a rotating cutting tool.
8.Can metal CNC machines be automated for continuous production?
Yes, metal CNC machines can be automated for continuous production. Automation can be achieved by using a CNC controller, which is a computer-controlled device that can be programmed to control the machine's movements and operations. Automation can also be achieved by using a robotic arm, which can be programmed to perform specific tasks. Automation can help to increase production efficiency and reduce costs.
9.What are the common applications of metal CNC machining in the medical industry?
1. Orthopedic Implants: Metal CNC machining is used to create orthopedic implants such as hip and knee replacements, spinal implants, and dental implants. 2. Surgical Instruments: Metal CNC machining is used to create precision surgical instruments such as scalpels, forceps, and clamps. 3. Medical Devices: Metal CNC machining is used to create medical devices such as stents, catheters, and pacemakers. 4. Prosthetics: Metal CNC machining is used to create prosthetic limbs and other body parts. 5. Diagnostic Equipment: Metal CNC machining is used to create diagnostic equipment such as MRI and CT scanners.
10.About metal cnc warranty
Metal CNC machines typically come with a warranty that covers parts and labor for a certain period of time. The length of the warranty varies depending on the manufacturer and the type of machine. Generally, warranties range from one to three years. Some manufacturers may also offer extended warranties for an additional fee. It is important to read the warranty carefully to understand what is covered and what is not.
11.What are the environmental impacts of using different coolants in metal CNC machining?
The environmental impacts of using different coolants in metal CNC machining depend on the type of coolant used. Generally, coolants used in metal CNC machining can be divided into two categories: water-soluble and oil-based. Water-soluble coolants are generally considered to be more environmentally friendly than oil-based coolants. They are biodegradable and do not contain hazardous chemicals. However, they can still cause environmental damage if not disposed of properly. Oil-based coolants are not biodegradable and can contain hazardous chemicals. They can also cause air and water pollution if not disposed of properly. Additionally, they can be flammable and can cause fires if not handled properly.
12.What safety precautions should be taken when changing tools in a CNC machine
? 1. Make sure the machine is powered off and the power cord is unplugged. 2. Wear protective gear such as safety glasses, gloves, and a face shield. 3. Secure the workpiece with clamps or other appropriate fixtures. 4. Disconnect any air lines or other connections to the machine. 5. Remove any loose tools or debris from the work area. 6. Make sure the tool holder is securely locked in place. 7. Use the appropriate wrench or other tool to loosen and remove the tool. 8. Inspect the tool for any damage or wear before installing it. 9. Make sure the tool is properly installed and securely tightened. 10. Reconnect any air lines or other connections to the machine. 11. Test the machine to make sure it is functioning properly.
13.Can metal CNC machines produce high-quality surface finishes?
Yes, metal CNC machines can produce high-quality surface finishes. CNC machines are capable of producing very precise and accurate parts with smooth surfaces. The quality of the surface finish depends on the type of tooling used, the speed and feed rate of the machine, and the type of material being machined.
14.How does the selection of the correct tool path affect the outcome of metal CNC machining?
The selection of the correct tool path is critical to the success of metal CNC machining. The tool path determines the direction and speed of the cutting tool, as well as the amount of material that is removed. If the wrong tool path is chosen, the machined part may not meet the desired specifications, or the cutting tool may be damaged. Additionally, the wrong tool path can lead to an inefficient machining process, resulting in increased production costs.
15.About metal cnc raw material procurement system
A metal CNC raw material procurement system is a computerized system that helps to streamline the process of purchasing raw materials for CNC machining. The system helps to automate the process of ordering, tracking, and managing the raw materials needed for CNC machining. It also helps to ensure that the right materials are ordered in the right quantities and at the right time. The system can also help to reduce costs associated with purchasing raw materials, as well as improve the efficiency of the CNC machining process.
16.How does the speed of the machine affect the production process?
The speed of the machine affects the production process by determining how quickly the production process can be completed. Faster machines can produce more products in a shorter amount of time, while slower machines will take longer to produce the same amount of products. Faster machines also allow for more efficient use of resources, as they can produce more products with fewer resources. Additionally, faster machines can reduce the amount of time needed for setup and changeover, which can help to reduce costs and improve efficiency.
17.About metal cnc production equipment
Metal CNC production equipment is a type of computer-controlled machinery used to produce metal parts and components. It is used in a variety of industries, including aerospace, automotive, medical, and industrial. CNC production equipment is capable of producing complex shapes and intricate details with high precision and accuracy. It is also capable of producing parts with tight tolerances and repeatability. CNC production equipment is used to produce parts for a variety of applications, including automotive, aerospace, medical, and industrial.
18.What is the role of the spindle speed in metal CNC machining?
The spindle speed is an important factor in metal CNC machining. It determines the speed at which the cutting tool moves across the material, and affects the quality of the finished product. A higher spindle speed will result in a faster cutting process, but can also cause the cutting tool to wear out faster. A lower spindle speed will result in a slower cutting process, but will also reduce the wear on the cutting tool. The spindle speed must be carefully adjusted to ensure the best results.
19.What is the role of coolant in reducing heat and friction during metal CNC machining?
Coolant plays an important role in reducing heat and friction during metal CNC machining. Coolant helps to reduce the temperature of the cutting tool and the workpiece, which helps to reduce the amount of heat generated during the machining process. Coolant also helps to reduce friction between the cutting tool and the workpiece, which helps to reduce wear and tear on the cutting tool and the workpiece. Additionally, coolant helps to flush away chips and debris from the cutting area, which helps to reduce the risk of clogging and jamming.
Tag:china cnc metal fabrication,cnc cut metal,cnc metal fabrication,metal milling cnc,custom cnc metal cutting